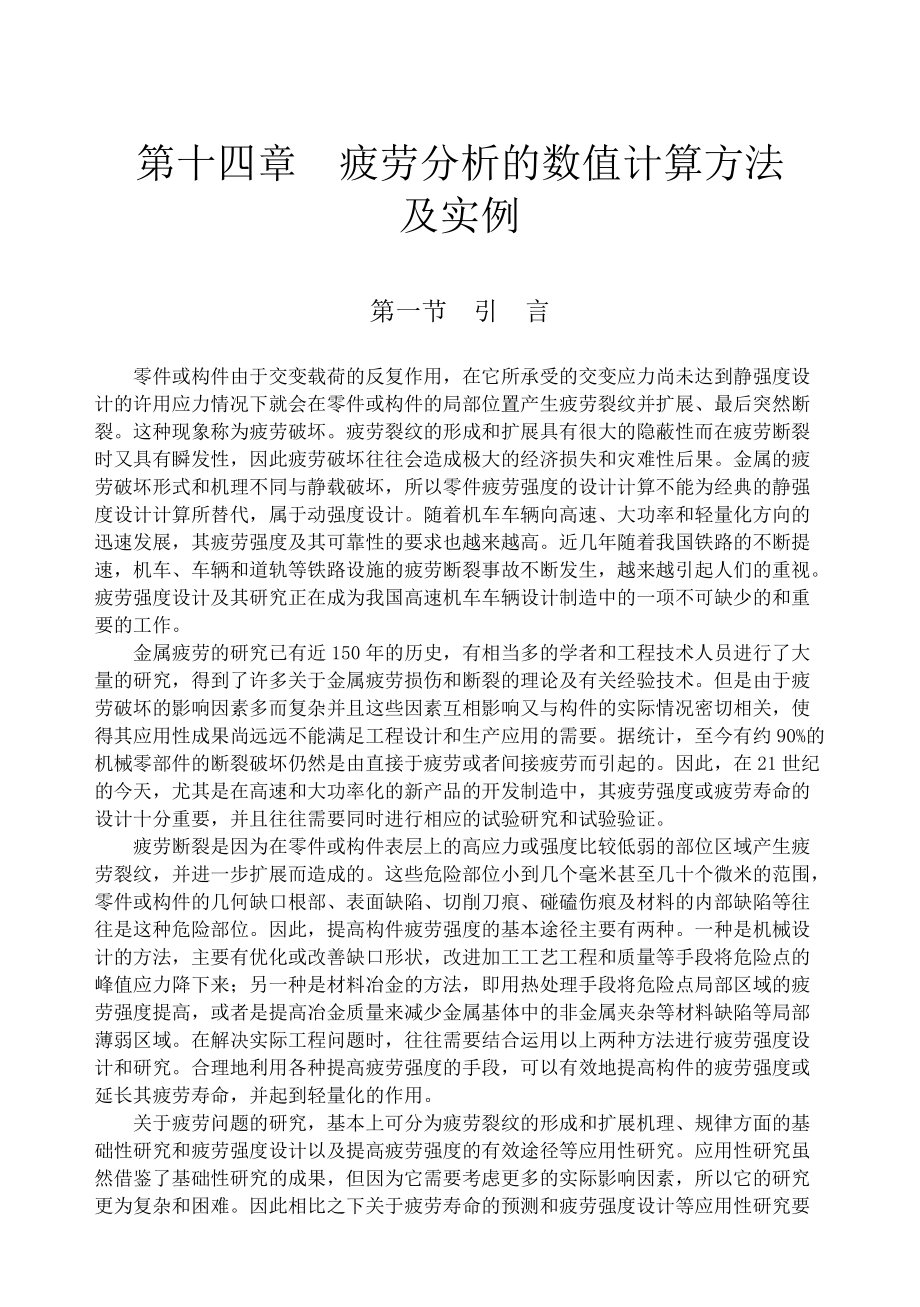




版權(quán)說明:本文檔由用戶提供并上傳,收益歸屬內(nèi)容提供方,若內(nèi)容存在侵權(quán),請進(jìn)行舉報(bào)或認(rèn)領(lǐng)
文檔簡介
1、第十四章 疲勞分析的數(shù)值計(jì)算方法及實(shí)例第一節(jié) 引 言零件或構(gòu)件由于交變載荷的反復(fù)作用,在它所承受的交變應(yīng)力尚未達(dá)到靜強(qiáng)度設(shè)計(jì)的許用應(yīng)力情況下就會(huì)在零件或構(gòu)件的局部位置產(chǎn)生疲勞裂紋并擴(kuò)展、最后突然斷裂。這種現(xiàn)象稱為疲勞破壞。疲勞裂紋的形成和擴(kuò)展具有很大的隱蔽性而在疲勞斷裂時(shí)又具有瞬發(fā)性,因此疲勞破壞往往會(huì)造成極大的經(jīng)濟(jì)損失和災(zāi)難性后果。金屬的疲勞破壞形式和機(jī)理不同與靜載破壞,所以零件疲勞強(qiáng)度的設(shè)計(jì)計(jì)算不能為經(jīng)典的靜強(qiáng)度設(shè)計(jì)計(jì)算所替代,屬于動(dòng)強(qiáng)度設(shè)計(jì)。隨著機(jī)車車輛向高速、大功率和輕量化方向的迅速發(fā)展,其疲勞強(qiáng)度及其可靠性的要求也越來越高。近幾年隨著我國鐵路的不斷提速,機(jī)車、車輛和道軌等鐵路設(shè)施的疲
2、勞斷裂事故不斷發(fā)生,越來越引起人們的重視。疲勞強(qiáng)度設(shè)計(jì)及其研究正在成為我國高速機(jī)車車輛設(shè)計(jì)制造中的一項(xiàng)不可缺少的和重要的工作。金屬疲勞的研究已有近150年的歷史,有相當(dāng)多的學(xué)者和工程技術(shù)人員進(jìn)行了大量的研究,得到了許多關(guān)于金屬疲勞損傷和斷裂的理論及有關(guān)經(jīng)驗(yàn)技術(shù)。但是由于疲勞破壞的影響因素多而復(fù)雜并且這些因素互相影響又與構(gòu)件的實(shí)際情況密切相關(guān),使得其應(yīng)用性成果尚遠(yuǎn)遠(yuǎn)不能滿足工程設(shè)計(jì)和生產(chǎn)應(yīng)用的需要。據(jù)統(tǒng)計(jì),至今有約90%的機(jī)械零部件的斷裂破壞仍然是由直接于疲勞或者間接疲勞而引起的。因此,在21世紀(jì)的今天,尤其是在高速和大功率化的新產(chǎn)品的開發(fā)制造中,其疲勞強(qiáng)度或疲勞壽命的設(shè)計(jì)十分重要,并且往往需要
3、同時(shí)進(jìn)行相應(yīng)的試驗(yàn)研究和試驗(yàn)驗(yàn)證。疲勞斷裂是因?yàn)樵诹慵驑?gòu)件表層上的高應(yīng)力或強(qiáng)度比較低弱的部位區(qū)域產(chǎn)生疲勞裂紋,并進(jìn)一步擴(kuò)展而造成的。這些危險(xiǎn)部位小到幾個(gè)毫米甚至幾十個(gè)微米的范圍,零件或構(gòu)件的幾何缺口根部、表面缺陷、切削刀痕、碰磕傷痕及材料的內(nèi)部缺陷等往往是這種危險(xiǎn)部位。因此,提高構(gòu)件疲勞強(qiáng)度的基本途徑主要有兩種。一種是機(jī)械設(shè)計(jì)的方法,主要有優(yōu)化或改善缺口形狀,改進(jìn)加工工藝工程和質(zhì)量等手段將危險(xiǎn)點(diǎn)的峰值應(yīng)力降下來;另一種是材料冶金的方法,即用熱處理手段將危險(xiǎn)點(diǎn)局部區(qū)域的疲勞強(qiáng)度提高,或者是提高冶金質(zhì)量來減少金屬基體中的非金屬夾雜等材料缺陷等局部薄弱區(qū)域。在解決實(shí)際工程問題時(shí),往往需要結(jié)合運(yùn)用以
4、上兩種方法進(jìn)行疲勞強(qiáng)度設(shè)計(jì)和研究。合理地利用各種提高疲勞強(qiáng)度的手段,可以有效地提高構(gòu)件的疲勞強(qiáng)度或延長其疲勞壽命,并起到輕量化的作用。關(guān)于疲勞問題的研究,基本上可分為疲勞裂紋的形成和擴(kuò)展機(jī)理、規(guī)律方面的基礎(chǔ)性研究和疲勞強(qiáng)度設(shè)計(jì)以及提高疲勞強(qiáng)度的有效途徑等應(yīng)用性研究。應(yīng)用性研究雖然借鑒了基礎(chǔ)性研究的成果,但因?yàn)樗枰紤]更多的實(shí)際影響因素,所以它的研究更為復(fù)雜和困難。因此相比之下關(guān)于疲勞壽命的預(yù)測和疲勞強(qiáng)度設(shè)計(jì)等應(yīng)用性研究要少得多,遠(yuǎn)遠(yuǎn)落后于實(shí)際工程的需求。過去,疲勞強(qiáng)度設(shè)計(jì)和壽命預(yù)測的研究主要是以試驗(yàn)為基礎(chǔ)進(jìn)行的。隨著計(jì)算機(jī)應(yīng)用技術(shù)和有限元數(shù)值計(jì)算理論及其應(yīng)用的迅速發(fā)展,現(xiàn)在又興起了基于大量試
5、驗(yàn)數(shù)據(jù)的疲勞強(qiáng)度設(shè)計(jì)和壽命計(jì)算的有限元數(shù)值計(jì)算方法,有力地推動(dòng)著零部件疲勞強(qiáng)度設(shè)計(jì)的研究及應(yīng)用的發(fā)展。當(dāng)前,業(yè)已發(fā)展形成了專用的疲勞分析軟件,如MSC/FATIGUE等。此外許多著名的有限元分析軟件也嵌套有功能較為齊全的疲勞強(qiáng)度計(jì)算模塊,如MARC,ANSYS,以及I-Deas中的CAE等。這些軟件疲勞強(qiáng)度計(jì)算模塊的細(xì)節(jié)雖然不盡相同,但是其基本思路與算法大都相似。本章將闡述疲勞強(qiáng)度設(shè)計(jì)的基本概念、疲勞強(qiáng)度的主要影響因素、疲勞強(qiáng)度設(shè)計(jì)的有關(guān)理論、基本設(shè)計(jì)方法等。最后,還將對疲勞強(qiáng)度分析的實(shí)例進(jìn)行介紹。第二節(jié) 疲勞載荷類型與S-N曲線:一、疲勞載荷的類型與基本術(shù)語使零件或構(gòu)件發(fā)生疲勞破壞的動(dòng)載荷稱
6、為疲勞載荷,可分為為兩類。一類是其大小和正負(fù)方向隨時(shí)間周期性地變化的交變載荷,另一類是大小和正負(fù)方向隨時(shí)間隨機(jī)變化的隨機(jī)載荷。交變載荷又稱為循環(huán)載荷,是最為簡單和基本的疲勞載荷形式。所研究結(jié)構(gòu)部位因交變載荷引起的應(yīng)力稱為交變應(yīng)力。圖14-1(a)是一個(gè)典型的交變應(yīng)力-時(shí)間的變化歷程。圖中循環(huán)應(yīng)力的大小和正負(fù)方(拉壓)向隨著時(shí)間的變化而作周期性的變化。一個(gè)周期的應(yīng)力變化過程稱為一個(gè)應(yīng)力循環(huán)。應(yīng)力循環(huán)特點(diǎn)可用循環(huán)中的最大應(yīng)力max、最小應(yīng)力min和周期T(或頻率f=1/T)來描述。因?yàn)樽畲髴?yīng)力和最小應(yīng)力的絕對值相等而正負(fù)號相反,故稱這種交變載荷為對稱循環(huán)應(yīng)力。典型的循環(huán)載荷如圓軸類桿件的旋轉(zhuǎn)彎曲、
7、軸向拉壓和平板零件的雙向彎曲等,都可以在零件的表面或內(nèi)部產(chǎn)生這樣的交變應(yīng)力。另外,軸類零件的雙向扭轉(zhuǎn)也可以產(chǎn)生類似的交變應(yīng)力。0minmaxat0maxminamt圖14-1(a) 對稱循環(huán)交變載荷圖14-1(b) 不對稱循環(huán)交變載荷在疲勞載荷的描述中經(jīng)常使用應(yīng)力幅a和應(yīng)力范圍(也稱為應(yīng)力振幅、應(yīng)力幅度)的概念,定義如下。 (14-1) (14-2)應(yīng)力幅a反映了交變應(yīng)力在一個(gè)應(yīng)力循環(huán)中變化大小的程度,它是使金屬構(gòu)件發(fā)生疲勞破壞的根本原因。當(dāng)研究的部位除承受有動(dòng)載荷外,還有靜載分量荷時(shí),動(dòng)靜載荷的共同作用下的應(yīng)力-時(shí)間變化曲線如圖14-1(b)所示。此時(shí)的載荷時(shí)間-變化曲線相當(dāng)于把圖14-1(
8、a)的對稱循環(huán)應(yīng)力曲線向上平移一個(gè)了靜應(yīng)力分量。這種的循環(huán)載荷稱為不對稱循環(huán)載荷,并用最小應(yīng)力與最大應(yīng)力的比值R來描述循環(huán)應(yīng)力的不對稱程度,R稱為應(yīng)力比,有時(shí)又稱為不對稱系數(shù),即 (14-4)由定義可知,當(dāng)R=-1時(shí)的循環(huán)應(yīng)力即為對稱循環(huán)應(yīng)力,當(dāng)R0時(shí)統(tǒng)稱不對稱循環(huán)應(yīng)力。其中,R=0時(shí)為拉伸脈動(dòng)應(yīng)力,R=-時(shí)為壓縮脈動(dòng)循環(huán)。循環(huán)應(yīng)力中的靜載分量通常稱為平均應(yīng)力,用m表示,可由下式求出。 (14-5)靜載分量或平均應(yīng)力對構(gòu)件的疲勞強(qiáng)度有一定的影響。壓縮平均應(yīng)力往往提高構(gòu)件的疲勞強(qiáng)度,而拉伸平均應(yīng)力往往降低構(gòu)件的疲勞強(qiáng)度。因此,在疲勞強(qiáng)度和疲勞壽命的研究中,給定一個(gè)循環(huán)應(yīng)力水平時(shí),需要同時(shí)給出應(yīng)力
9、幅a和應(yīng)力比R、或者同時(shí)給出最大應(yīng)力max和平均應(yīng)力m,也有時(shí)直接給出最大應(yīng)力max和最小應(yīng)力min來表示循環(huán)應(yīng)力水平。由以上各式可知,在應(yīng)力幅、平均應(yīng)力、應(yīng)力比、最大應(yīng)力和最小應(yīng)力的參數(shù)中,只要已知其中的兩個(gè)便可求出其它。如當(dāng)已知a、R時(shí),其它參數(shù)便可由下式得到。 (14-6)或者已知或a、m時(shí), (14-7)二、材料的S-N曲線與基本術(shù)語一般情況下,材料所承受的循環(huán)載荷的應(yīng)力幅越小,到發(fā)生疲勞破斷時(shí)所經(jīng)歷的應(yīng)力循環(huán)次數(shù)越長。S-N曲線就是材料所承受的應(yīng)力幅水平與該應(yīng)力幅下發(fā)生疲勞破壞時(shí)所經(jīng)歷的應(yīng)力循環(huán)次數(shù)的關(guān)系曲線。S-N曲線一般是使用標(biāo)準(zhǔn)試樣進(jìn)行疲勞試驗(yàn)獲得的。如圖14-2所示,縱坐標(biāo)表
10、示試樣承受的應(yīng)力幅,有時(shí)也表示為最大應(yīng)力,但二者一般都用表示;橫坐標(biāo)表示應(yīng)力循環(huán)次數(shù),常用Nf表示。為使用方便,在雙對數(shù)坐標(biāo)系下S-N曲線被近似簡化成兩條直線。但也有很多情況只對橫坐標(biāo)取對數(shù),此時(shí)也常把S-N曲線近似簡化成兩條直線。S-N曲線中的水平直線部分對應(yīng)的應(yīng)力水平就是材料的疲勞極限,其原意為材料經(jīng)受無N-1圖14-2S-N疲勞曲線數(shù)次應(yīng)力循環(huán)都不發(fā)生破壞的應(yīng)力極限,對鋼鐵材料此“無限”的定義一般為107次應(yīng)力循環(huán)。但現(xiàn)代高速疲勞試驗(yàn)機(jī)的研究成果表明,即使應(yīng)力循環(huán)次數(shù)超過107材料仍然有可能發(fā)生疲勞斷裂。不過107次的應(yīng)力循環(huán)次數(shù),對于實(shí)際的工程中的疲勞強(qiáng)度設(shè)計(jì)已經(jīng)完全能夠滿足需要。疲勞
11、極限又稱持久極限,對于無缺口的光滑試樣,多用w0表示,而應(yīng)力比R=-1時(shí)的疲勞極限常用-1來表示。某些不銹鋼和有色金屬的S-N中沒有水平直線部分,此時(shí)的疲勞極限都一般定義為108次應(yīng)力循環(huán)下對應(yīng)的應(yīng)力幅水平。疲勞極限是材料抗疲勞能力的重要性能指標(biāo),也是進(jìn)行疲勞強(qiáng)度的無限壽命設(shè)計(jì)的主要依據(jù)。斜線部分給出了試樣承受的應(yīng)力幅水平與發(fā)生疲勞破斷時(shí)所經(jīng)歷的應(yīng)力循環(huán)次數(shù)之間的關(guān)系,多用如冪函數(shù)的形式表示。 (14-8)式中為應(yīng)力幅或最大應(yīng)力,N為達(dá)到疲勞破斷時(shí)的應(yīng)力循環(huán)次數(shù),m,C材料常數(shù)。如果給定一個(gè)應(yīng)力循環(huán)次數(shù),便可由上式求出或由斜線量出材料在該條件下所能承受的最大應(yīng)力幅水平。反之,也可以由一定的工作
12、應(yīng)力幅求出對應(yīng)的疲勞壽命。因?yàn)榇藭r(shí)試樣或材料所能承受的應(yīng)力幅水平是與給定的應(yīng)力循環(huán)次數(shù)相關(guān)聯(lián)的,所以稱之為條件疲勞極限,或稱為疲勞強(qiáng)度。斜線部分是零部件疲勞強(qiáng)度的有限壽命設(shè)計(jì)或疲勞壽命計(jì)算的主要依據(jù)。材料或構(gòu)件到發(fā)生疲勞破壞時(shí)所經(jīng)歷的應(yīng)力循環(huán)次數(shù)稱為材料或構(gòu)件的疲勞壽命,通常它包括疲勞裂紋的萌生壽命與擴(kuò)展壽命之和。疲勞裂紋萌生壽命為構(gòu)件從開始使用到局部區(qū)域產(chǎn)生疲勞損傷累積、萌生裂紋時(shí)的壽命;裂紋擴(kuò)展壽命為構(gòu)件在裂紋萌生后繼續(xù)使用而導(dǎo)致裂紋擴(kuò)展達(dá)到疲勞破壞時(shí)的壽命。在疲勞強(qiáng)度設(shè)計(jì)中,疲勞破壞可能被定義為疲勞破斷或規(guī)定的報(bào)廢限度。S-N曲線又稱為應(yīng)力-壽命曲線,主要用于構(gòu)件的變形在彈性變形范圍內(nèi)的
13、情形。一般說來,這種應(yīng)力狀態(tài)下的疲勞達(dá)到破壞時(shí)的循環(huán)次數(shù)比較高,往往達(dá)到106以上,所以這種疲勞又稱為高周疲勞。相對地,達(dá)到疲勞破壞的循環(huán)次數(shù)較低時(shí)的疲勞稱為低周疲勞,發(fā)生低周疲勞時(shí)構(gòu)件在局部位置發(fā)生了塑性變形。近三十年來,對于低周疲勞,基于塑性應(yīng)變幅a的疲勞壽命曲線(a-N)在工程中得到應(yīng)用。對于帶缺口的零件,其工作載荷變動(dòng)較大時(shí),在應(yīng)力集中的局部區(qū)域?qū)?huì)發(fā)生塑性變形,此時(shí)疲勞壽命估算則要求基于應(yīng)力和基于塑性應(yīng)變的兩種材料疲勞性能曲線。這種方法目前還不能用于高周疲勞的壽命估算。第三節(jié)、疲勞強(qiáng)度的影響因素通常我們通過手冊所獲得的S-N曲線大多是無缺口的標(biāo)準(zhǔn)試樣的試驗(yàn)結(jié)果。但是實(shí)際零部件的形狀、
14、尺寸、表面狀態(tài)、工作環(huán)境和工作載荷的特點(diǎn)都可能大不相同,而這些因素都對零部件的疲勞強(qiáng)度產(chǎn)生很大的影響。疲勞強(qiáng)度的影響因素可分為力學(xué)、冶金學(xué)和環(huán)境三個(gè)方面。這些因素互相聯(lián)系影響,使得在疲勞強(qiáng)度設(shè)計(jì)和疲勞壽命預(yù)測時(shí),綜合評價(jià)這些因素影響變得復(fù)雜。三類因素中,力學(xué)因素從根本上講可歸結(jié)為應(yīng)力集中和平均應(yīng)力的影響;冶金學(xué)因素可歸納為冶金質(zhì)量即材料的純凈度和材料的強(qiáng)度;而環(huán)境因素主要有腐蝕介質(zhì)和高溫的影響。對于鐵路車輛零部件大多數(shù)的情況是在大氣和常溫環(huán)境下工作的,所以一般情況下應(yīng)主要考慮力學(xué)和冶金學(xué)兩類因素。它們包括缺口形狀的影響、尺寸的影響、表面狀態(tài)的影響和平均應(yīng)力的影響等。關(guān)于這些因素對疲勞極限影響的
15、具體數(shù)據(jù)相關(guān)的經(jīng)驗(yàn)公式,可查閱有關(guān)手冊和資料。這里主要討論疲勞強(qiáng)度設(shè)計(jì)和疲勞壽命預(yù)測時(shí)需要了解的一些比較重要的影響規(guī)律或現(xiàn)象,以及必須或應(yīng)該考慮到的注意事項(xiàng)。一、缺口形狀效應(yīng)零件或構(gòu)件常常帶有如軸肩類的臺階、螺栓孔和油孔、鍵槽等所謂的缺口。如圖2-1所示,它們的共同特點(diǎn)是零件的橫截面積在缺口處發(fā)生了突變,而在這些缺口根部應(yīng)力會(huì)急劇升高,這種現(xiàn)象叫做應(yīng)力集中。缺口處的應(yīng)力集中是造成零部件疲勞強(qiáng)度大幅度下降的最主要的因素。應(yīng)力集中使得缺口根部的實(shí)際應(yīng)力遠(yuǎn)大于名義應(yīng)力,使該處產(chǎn)生疲勞裂紋,最終導(dǎo)致零件失效或破壞。應(yīng)力集中的程度用應(yīng)力集中系數(shù)(又稱理論應(yīng)力集中系數(shù))Kt來描述,表達(dá)式如下。 (14-9
16、)這里,max為最大應(yīng)力,0為載荷除以缺口處凈截面積所的得平均應(yīng)力,又稱名義應(yīng)力。在一定范圍內(nèi),缺口根部的曲率半徑越小,應(yīng)力集中程度越大,疲勞強(qiáng)度降低的程度也就越大。但是,對于低中碳鋼等塑性材料,當(dāng)缺口根部的曲率半徑進(jìn)一步減小甚至小于零點(diǎn)幾個(gè)毫米時(shí),疲勞強(qiáng)度的降低程度會(huì)變的越來越小甚至不再降低。此時(shí)應(yīng)力集中系數(shù)就無法真實(shí)地反映缺口對疲勞強(qiáng)度的影響。因此常用疲勞缺口系數(shù)Kf(fatigue notch factor,過去又被稱為有效應(yīng)力集中系數(shù))來更直接地反映疲勞強(qiáng)度的真實(shí)的降低程度。 (14-10)這里,w0,w分別為無缺口光滑試樣和缺口試樣的疲勞極限。圖14-4為鋼的應(yīng)力集中系數(shù)Kt與疲勞缺
17、口系數(shù)Kf之間的關(guān)系。由圖可見,對于低中碳鋼,在應(yīng)力集中系數(shù)小于22.5時(shí)Kt與Kf基本相同,但當(dāng)超過此數(shù)值時(shí),Kf的增長速度明顯變慢。而對于高碳鋼等強(qiáng)度比較高的鋼,Kf隨Kt線性遞增的關(guān)系保持很長的范圍。由此可知,高強(qiáng)度鋼的疲勞強(qiáng)度對缺口的敏感性高而低中強(qiáng)度鋼的疲勞強(qiáng)度對缺口的敏感性較低。一般情況下,KfKt,但對于高碳鋼尖銳缺口,還有可能存在KtKf的現(xiàn)象。對于螺栓類零件也存在這種現(xiàn)象,有時(shí)出現(xiàn)Kt為約4左右而Kf為810的情況。這主要是因?yàn)槊總€(gè)螺紋所分擔(dān)的載荷不均甚至載荷幾種在某扣螺紋上所致。對于光滑材料,通過表面淬火、表面滲碳、表面氮化等表面熱處理可以有效地提高其疲勞強(qiáng)度。但是對于缺口
18、材料,這些方法可能變的沒有效果甚至使疲勞強(qiáng)度反而降低。這是因?yàn)橥ㄟ^熱處理使其表面強(qiáng)度提高的同時(shí),使缺口敏感性也變高的緣故。圖14-5為高強(qiáng)度鋼和塑性較好的低強(qiáng)度鋼的缺口材料的疲勞強(qiáng)度隨應(yīng)力集中程度的增加而變化的情況。在應(yīng)力集中Kt較小的范圍內(nèi),高強(qiáng)度鋼的疲勞強(qiáng)度明顯比低強(qiáng)度鋼的高。但隨著應(yīng)力集中系數(shù)的增加,高強(qiáng)度鋼的疲勞強(qiáng)度的降低速度明顯大于低強(qiáng)度鋼者,以致于高強(qiáng)度鋼的疲勞強(qiáng)度與低強(qiáng)度鋼的疲勞強(qiáng)度相差無幾。對于焊接構(gòu)件,由于焊接熱影響區(qū)在許多情況下恰好處于結(jié)構(gòu)性缺口部位或在其附近,加之焊接缺陷、焊接殘余拉應(yīng)力的作用等,使得疲勞強(qiáng)度可能大幅下降幾倍甚至十幾倍。疲勞缺口系數(shù)還受零部件尺寸大小的影響
19、,一般地在具有相同缺口的情況下,隨著尺寸的增大其疲勞缺口系數(shù)也有所增大。因此對于缺口材料或帶有缺口的零部件,為了提高其疲勞壽命,最有效的方法是合理地疲勞缺口系數(shù)KfKf=KtNiCr600退火0.21%碳素鋼0.38%碳素鋼0.76%碳素鋼NiCr400退火応力集中系數(shù)Kt圖14-4 鋼的應(yīng)力集中系數(shù)Kt與疲勞缺口系數(shù)K的關(guān)系0123淬火回火退火應(yīng)力集中系數(shù)Kt疲勞缺口系數(shù)Kf圖14-5 缺口材料的疲勞強(qiáng)度隨應(yīng)力集中程度的變化進(jìn)行結(jié)構(gòu)設(shè)計(jì)和工藝選擇等手段來設(shè)法降低或改進(jìn)它的應(yīng)力集中情況。而一味地選用高強(qiáng)度鋼材,未必能夠達(dá)到目的,相反在表面較粗糙和尺寸較大的情況下有可能反而使構(gòu)件的疲勞強(qiáng)度下降。
20、二、零件尺寸效應(yīng)用于疲勞試驗(yàn)的式樣的直徑一般都在510mm的范圍內(nèi),這和實(shí)際零部件的尺寸有很大的差異。一般地,對于彎曲和扭轉(zhuǎn)載荷下的零件,隨著尺寸的增大疲勞強(qiáng)度降低。但是對于軸向拉伸和壓縮載荷的情況,尺寸大小的影響不大。尺寸對疲勞極限影響的大小用尺寸影響系數(shù)來表示。 (14-11)這里,d,d0分別為任意尺寸和標(biāo)準(zhǔn)尺寸光滑試樣的疲勞極限。高強(qiáng)度鋼的尺寸效應(yīng)比低強(qiáng)度鋼的尺寸效應(yīng)大,表面粗糙的零件的尺寸效應(yīng)較大。尺寸效應(yīng)的產(chǎn)生主要是因?yàn)檩^大尺寸的材料的組織狀態(tài)和應(yīng)力梯度對疲勞強(qiáng)度產(chǎn)生了影響。材料的尺寸越大制造工藝過程越難控制,材料組織的致密性和均勻性等越差、冶金缺陷越多,表面積越大這些缺陷的數(shù)量也
21、越多,因此大尺寸試樣表面產(chǎn)生疲勞、裂紋的機(jī)會(huì)也就越大。而這些從根本上來說又都可以歸結(jié)為冶金缺陷造成了局部應(yīng)力集中而導(dǎo)致了疲勞裂紋的產(chǎn)生。關(guān)于應(yīng)力梯度的影響,在承受彎曲、扭轉(zhuǎn)等載荷的情況下,零件的尺寸越大工作應(yīng)力的梯度越小,單位面積內(nèi)的平均應(yīng)力就越高,疲勞裂紋越易產(chǎn)生。三、表面狀況的影響表面狀況包括表面粗糙度、表面應(yīng)力狀態(tài)、表面塑性變形程度和表面缺陷等因素。在試驗(yàn)中采用的是表面磨光(或拋光)的標(biāo)準(zhǔn)試樣,但實(shí)際的零部件的表面則往往是機(jī)械加工表面鍛造表面和鑄造表面。機(jī)械加工會(huì)在零件表面產(chǎn)生塑性加工硬化。切削加工往往會(huì)在零件表面產(chǎn)生一定的殘余壓應(yīng)力,這對疲勞強(qiáng)度是有利的但效果有限。但是在磨削時(shí)往往會(huì)產(chǎn)
22、生對疲勞強(qiáng)度不利的殘余拉應(yīng)力。另一方面,機(jī)械加工表面的顯微尺度上的凸凹不平引會(huì)起應(yīng)力集中而使疲勞強(qiáng)度降低。這些因素綜合作用的結(jié)果,使疲勞強(qiáng)度比標(biāo)準(zhǔn)試樣的要降低一些。而鍛造或鑄造表面一般具有更高的表面粗糙度,且部存在表面加工硬化層和表面殘余壓應(yīng)力,因此會(huì)更加明顯地降低疲勞強(qiáng)度。因此從形式上看,越是粗糙的表面加工方法,對疲勞強(qiáng)度的降低影響就越大。表面加工狀況對疲勞強(qiáng)度的影響用表面加工系數(shù)來表示。 (14-12)這里,為某種表面狀態(tài)下標(biāo)準(zhǔn)光滑試樣的疲勞極限,0為磨光標(biāo)準(zhǔn)光滑試樣的疲勞極限,國外為表面磨光的標(biāo)準(zhǔn)光滑試樣。從冶金角度看,粗加工對高強(qiáng)度材料的疲勞強(qiáng)度的影響更大,以至于在粗加工狀態(tài)下高強(qiáng)度鋼
23、可能起不到絲毫的提高疲勞強(qiáng)度的作用。這主要是因?yàn)楦邚?qiáng)度材料對粗糙表面的缺口敏感性高的緣故,加之機(jī)械加工對于高強(qiáng)度鋼的表面的加工硬化作用也很小。關(guān)于表面脫碳、表面碰磕傷痕和劃傷等表面缺陷等對疲勞強(qiáng)度的影響的研究較少,但這些偶然原因造成的表面缺陷會(huì)對疲勞強(qiáng)度造成很大的影響。因此,在設(shè)計(jì)尤其是制造過程中需要給予足夠的重視。對于光滑材料,表面熱處理等表面改性方法可以提高疲勞強(qiáng)度,但對于實(shí)際零部件等帶有缺口的材料,這些方法都效果不大,甚至產(chǎn)生相反的作用。因此多用噴丸、輥壓的方法使表面產(chǎn)生加工硬化和殘余壓應(yīng)力,從而提高構(gòu)件的疲勞強(qiáng)度,但是這兩種方法一般對孔口類缺口的零件的疲勞強(qiáng)度的提高作用并不明顯。最新的
24、研究表明,用簡單的金屬模具對孔口邊緣進(jìn)行少量倒角從而使缺口部位殘生局部塑性變形的方法,對疲勞強(qiáng)度有明顯的提高,甚至可以完全消除缺口降低疲勞極限的影響。過去大多認(rèn)為,表面塑性加工的方法提高疲勞強(qiáng)度的主要原因是在表面產(chǎn)生了殘余壓應(yīng)力從而抵消了部分工作應(yīng)力的緣故。實(shí)際上是殘余壓應(yīng)力在缺口部位產(chǎn)生的壓縮集中應(yīng)力抵消了缺口的不利影響;塑性變形使得缺口附近組織中的微小薄弱區(qū)域得到強(qiáng)化,使組織性能變的更加均勻一致,整體強(qiáng)度得到提高,從而使產(chǎn)生疲勞裂紋的應(yīng)力水平得到提高。同時(shí),殘余壓應(yīng)力還使疲勞裂紋擴(kuò)展停止而成為停留裂紋。四、平均應(yīng)力的影響 如前所述,產(chǎn)生疲勞破壞的根本原因是動(dòng)應(yīng)力分量,但靜應(yīng)力分量即平均應(yīng)力
25、對疲勞極限也有一定的影響。在一定的靜應(yīng)力范圍內(nèi),壓縮的靜應(yīng)力提高疲勞極限,拉伸的靜應(yīng)力降低疲勞極限。一般認(rèn)為,殘余應(yīng)力對疲勞極限的作用同平均應(yīng)力的作用相同。對一種材料, 可根據(jù)它在各種平均應(yīng)力或應(yīng)力比R下的疲勞極限結(jié)果畫出疲勞極限圖。圖14-6的橫坐標(biāo)為平均應(yīng)力m(或殘余應(yīng)力)和強(qiáng)度極限b的比值,縱坐標(biāo)為應(yīng)力圖14-6 鋼在107次循環(huán)壽命下的疲勞極限線圖幅a和對稱循環(huán)疲勞極限-1的比值,兩者都是無量綱的量。從圖中可以看出,多數(shù)試驗(yàn)數(shù)據(jù)點(diǎn)落在直線與曲線之間。這條直線稱為古德曼(Goodman)線,見式(14-13);曲線就是杰柏(Gerber)拋物線,見式(14-14);用屈服極限s代替b得到
26、索德柏格(Soderberg)線,見式(14-15);用斷裂真應(yīng)力f代替b,得到摩儒(Morrow)線,見式(14-16)。Goodman線 (14-13)Gerbe線 (14-14)Sodeberrg線 (14-15)Morrow線 (14-16)古德曼(Goodman)線對于延性金屬略偏保守且簡單方便,在疲勞設(shè)計(jì)中應(yīng)用最廣。常用的還有另一種叫做理想的改進(jìn)Goodman圖。圖14-7為工字形型鋼對接梁彎曲疲勞載荷下理想的改進(jìn)Goodman圖。橫坐標(biāo)表示最小應(yīng)力min,縱坐標(biāo)表示最大應(yīng)力max,其直線方程式為 (14-17)式中,m是Goodman線的斜率,b為直線在y軸上的截距,它是最小應(yīng)力
27、等于零時(shí)即脈動(dòng)循環(huán)的疲勞極限。疲勞極限用最大應(yīng)力表示時(shí),即w=max,考慮到應(yīng)力比R=max/min,由式(14-6)有min斜率=mbR=1R=-1-minmins圖14-7 理想的改進(jìn)Goodman圖(14-18)由式(14-18)即可求出應(yīng)力比為R時(shí)的疲勞極限。實(shí)際車輛的具體結(jié)構(gòu)要遠(yuǎn)比獲得S-N曲線時(shí)的試驗(yàn)條件復(fù)雜,例如焊接形式及應(yīng)力集中等等,美國AAR標(biāo)準(zhǔn)為我們提供了許多典型焊接結(jié)構(gòu)疲勞強(qiáng)度方面的有價(jià)值的參考,所以,實(shí)際計(jì)算中的b與m均取自于AAR標(biāo)準(zhǔn)。 試驗(yàn)研究表明,靜載分量對應(yīng)力集中系數(shù)、尺寸系數(shù)、表面系數(shù)的影響較小,可以忽略。第四節(jié) 疲勞強(qiáng)度設(shè)計(jì)通過設(shè)計(jì)計(jì)算來預(yù)測構(gòu)件或零件的疲勞
28、強(qiáng)度和疲勞壽命,是多少年來無數(shù)學(xué)者和工程技術(shù)人員孜孜以求的目標(biāo)。但是至今還沒能夠形成一種對實(shí)際工程適用的、比較準(zhǔn)確的疲勞強(qiáng)度和壽命的計(jì)算方法。這是因?yàn)?,研究對象在結(jié)構(gòu)上的千變?nèi)f化、加工制造工藝及其質(zhì)量的不穩(wěn)定性、材料組織性能不穩(wěn)定性和內(nèi)部及表面缺陷的不確定性、外部載荷的復(fù)雜和隨幾性以及結(jié)構(gòu)的動(dòng)態(tài)響應(yīng)問題等等,諸如這些因素很難歸納成為一個(gè)統(tǒng)一的物理或數(shù)學(xué)模型。因此至今關(guān)于疲勞強(qiáng)度的計(jì)算都有一定的誤差存在甚至誤差很。即使計(jì)算結(jié)果是比較準(zhǔn)確的,其結(jié)果也具有統(tǒng)計(jì)性,而不是針對每一個(gè)零部件而言。對于新產(chǎn)品的開發(fā),應(yīng)至少對于某些重要零部件等,同時(shí)進(jìn)行試驗(yàn)研究和試驗(yàn)驗(yàn)證。如果受試驗(yàn)條件等的限制,可以根據(jù)零部
29、件的特點(diǎn)進(jìn)行合理簡化來進(jìn)行模擬性試驗(yàn),這也是非常有用的。諸多紛雜的因素中,對于疲勞強(qiáng)度危害最大的是應(yīng)力集中。因此,從設(shè)計(jì)和制造的過程來看,危害最大的第一是結(jié)構(gòu)的不合理性;第二是工藝缺陷如焊接缺陷、機(jī)械加工缺陷、材料內(nèi)部缺陷,還包括偶然因素造成的表面?zhèn)鄣鹊龋坏谌遣牧系倪x擇。因此如果為提高疲勞強(qiáng)度,在設(shè)計(jì)和制造過程中最重要的就是降低應(yīng)力集中。對于實(shí)際零部件還需要注意的是,因?yàn)槠渫鶐в行螤钊笨?,所以未必選擇高強(qiáng)度鋼就可提高其疲勞強(qiáng)度。到目前為止,疲勞強(qiáng)度的設(shè)計(jì)實(shí)質(zhì)上還是基于大量試驗(yàn)結(jié)果的估算。近年來已經(jīng)出現(xiàn)了有關(guān)疲勞強(qiáng)度設(shè)計(jì)的專用軟件,使得這項(xiàng)工作的效率更高和更易趨于合理準(zhǔn)確,但對于它的使用同
30、樣需要具有一定的疲勞強(qiáng)度設(shè)計(jì)的經(jīng)驗(yàn)。疲勞強(qiáng)度設(shè)計(jì)包括疲勞安全系數(shù)的校核和疲勞壽命的估算兩項(xiàng)內(nèi)容。具體的設(shè)計(jì)計(jì)算方法有應(yīng)力-壽命法和局部應(yīng)力-應(yīng)變法。局部應(yīng)力應(yīng)變法目前還只適用于零部件的應(yīng)力集中處發(fā)生了塑性變形的低周疲勞。應(yīng)力-壽命設(shè)計(jì)法主要用于只發(fā)生彈性變形的高周疲勞,設(shè)計(jì)所用的基本參數(shù)是零部件危險(xiǎn)點(diǎn)處的名義應(yīng)力,所以這種方法又叫名義應(yīng)力法,它的研究和使用歷史較長,資料豐富,至今仍被廣泛使用。名義應(yīng)力法包括無限壽命設(shè)計(jì)和有限壽命設(shè)計(jì)兩種設(shè)計(jì)思路,本節(jié)只就名義應(yīng)力法的內(nèi)容進(jìn)行討論。名義應(yīng)力法的關(guān)鍵點(diǎn)也是它的難點(diǎn)有三,一是疲勞極限降低系數(shù)和應(yīng)力-壽命曲線的確定,二是危險(xiǎn)點(diǎn)應(yīng)力的確定計(jì)算,三是外載荷
31、的獲得。而要解決好這些問題計(jì)算和試驗(yàn)而這都不可偏廢。一、無限壽命設(shè)計(jì)法無限壽命設(shè)計(jì)法的基本思路是,使得零件或構(gòu)件的危險(xiǎn)部位的工作應(yīng)力低于其疲勞極限,從而保證它在設(shè)計(jì)的工作應(yīng)力下能夠長久工作而部發(fā)生破壞。當(dāng)零件的結(jié)構(gòu)比較簡單應(yīng)力集中較小時(shí),恒幅交變應(yīng)力、過載應(yīng)力小且次數(shù)很少時(shí)可用這種方法。對應(yīng)力集中較大的構(gòu)件使用該方法進(jìn)行疲勞強(qiáng)度設(shè)計(jì)將會(huì)使結(jié)構(gòu)變的粗大笨重。對于過載應(yīng)力較大且次數(shù)較多的交變載荷情況和隨幾載荷一般也不宜采用此種方法。(一)對稱循環(huán)載荷:R=-1,疲勞強(qiáng)度條件為正應(yīng)力 (14-19)剪應(yīng)力 (14-20)式中,n,n安全系數(shù);a,a應(yīng)力幅;-1,-1,-1D,-1D分別為對稱循環(huán)下材
32、料和零件的疲勞極限,且有 (14-21)式中,KD,KD是對稱循環(huán)下零件的疲勞強(qiáng)度降低系數(shù),它包含了前面討論的疲勞強(qiáng)度的諸影響因素。該系數(shù)的選擇無疑將對疲勞強(qiáng)度的估算產(chǎn)生很大的影響。它有多種計(jì)算用經(jīng)驗(yàn)表達(dá)式形式,現(xiàn)只列出比較常見的幾種。 (14-22) (14-23) (14-24)式中, K,K疲勞缺口系數(shù),尺寸系數(shù),表面加工系數(shù)。以上三式的主要不同點(diǎn)在于對表面加工系數(shù)的處理。第一式認(rèn)為、K、三者互不影響;第二式認(rèn)為隨著K的增加而減弱;第三式認(rèn)為隨著K/值增加而減小。從試用的情況來看,在K較低的范圍內(nèi)三者的差別不大。在K較大的情況下,第一式的結(jié)果偏大,而第二式的結(jié)果比第三式的結(jié)果略大。關(guān)于表
33、面粗糙度等表面加工情況對疲勞缺口系數(shù)的影響,未見到有關(guān)的研究報(bào)道。但參照多重缺口材料的疲勞缺口系數(shù)的研究結(jié)果推斷,隨著疲勞缺口變尖銳表面粗糙度的影響不應(yīng)增大??紤]材料強(qiáng)度對表面加工系數(shù)的影響,高強(qiáng)度鋼適合采用第二式,而對于塑性比較好的低中強(qiáng)度鋼適合采用第三式。(二)不對稱循環(huán)載荷:1R保持不變時(shí)的疲勞強(qiáng)度條件為正應(yīng)力 (14-25)剪應(yīng)力 (14-26)式中,aD,aD應(yīng)力比為R時(shí)的疲勞極限;m,m平均應(yīng)力;,平均應(yīng)力折算系數(shù),對于Goodman方程(14-13)有=m/b,其它符號意義同上。2平均應(yīng)力保持不變時(shí): (14-27)式中符號意義同上。二、有限壽命設(shè)計(jì)法當(dāng)交變載荷有較多的沖擊過載或
34、工作載荷為隨幾載荷時(shí),工作應(yīng)力在某些時(shí)刻會(huì)越過疲勞極限。此時(shí),疲勞壽命設(shè)計(jì)主要是保證構(gòu)件在設(shè)計(jì)的壽命之內(nèi)不發(fā)生疲勞破壞而正常工作,也即設(shè)計(jì)使構(gòu)件具有有限的疲勞壽命??紤]到偶然因素的影響,為確保安全在設(shè)計(jì)時(shí)一般使設(shè)計(jì)壽命為使用壽命的數(shù)倍。有限壽命設(shè)計(jì)法主要基于疲勞累積損傷理論,故先作簡單介紹然后討論疲勞強(qiáng)度校核問題。(一)邁因納累積損傷理論:金屬疲勞累積損傷的假說多達(dá)數(shù)十種,但其中最簡單、適用的是邁因納(PalmgrenMiner)理論,習(xí)慣稱之為線性累積損傷理論。邁因納理論認(rèn)為材料的疲勞破壞是由于循環(huán)載荷的不斷作用而產(chǎn)生損傷并不斷積累造成的;疲勞損傷累積達(dá)到破壞時(shí)吸收的凈功W與疲勞載荷的歷史無
35、關(guān),并且材料的疲勞損傷程度與應(yīng)力循環(huán)次數(shù)成正比。設(shè)材料在某級應(yīng)力下達(dá)到破壞時(shí)的應(yīng)力循環(huán)次數(shù)為N1、經(jīng)n1次應(yīng)力循環(huán)而疲勞損傷吸收的凈功為W1,根據(jù)邁因納理論有則在i個(gè)應(yīng)力水平級別下分別對應(yīng)經(jīng)過ni次應(yīng)力循環(huán)時(shí),材料疲勞累積損傷為 (14-28)式中,ni第i級應(yīng)力水平下經(jīng)過的應(yīng)力循環(huán)數(shù);Ni第i級應(yīng)力水平下的達(dá)到破壞時(shí)的應(yīng)力循環(huán)數(shù)。當(dāng)D值等于1時(shí),認(rèn)為被評估對象開始破壞。應(yīng)該指出邁因納理論沒有考慮加載順序的影響和平均應(yīng)力的影響,只是一種近似理論。但是,由于該理論簡單便于利用,在工程上得到了廣泛應(yīng)用。針線性累積損傷理論所存在的問題,又提出了非線性累積損傷理論以提高其計(jì)算精度,但應(yīng)用不如前者廣。(
36、二)隨幾載荷的處理零部件承受的變幅載荷尤其是對承受隨幾載荷實(shí)需要測得到。利用累積損傷理論進(jìn)行疲勞設(shè)計(jì)時(shí),需要先對實(shí)測得到的載荷-時(shí)間歷程進(jìn)行編譜,即用概率統(tǒng)計(jì)的方法將其簡化成典型的載荷譜或應(yīng)力譜。因?yàn)橐鹌诘淖罡镜脑蚴莿?dòng)載分量應(yīng)力幅值和它的循環(huán)次數(shù),所以一般用統(tǒng)計(jì)記數(shù)法來處理波形與頻次的關(guān)系等問題。在各種統(tǒng)計(jì)記數(shù)法中,被國際上廣泛用于疲勞強(qiáng)度設(shè)計(jì)的是雨流計(jì)數(shù)法,它被認(rèn)為最符合材料的疲勞損傷規(guī)律。這種方法把整個(gè)載荷-時(shí)間歷程中出現(xiàn)的應(yīng)力幅范圍劃分為若干個(gè)等差的應(yīng)力幅級別,然后統(tǒng)計(jì)出各級應(yīng)力幅級別內(nèi)所出現(xiàn)的循環(huán)次數(shù),從而得到載荷-頻次曲線等各種形式的載荷的統(tǒng)計(jì)結(jié)果。實(shí)測的載荷-時(shí)間歷程的半波
37、數(shù)往往是數(shù)以幾十萬、幾百萬個(gè),用手算的方法幾乎是不可能的。所以工程上編制了雨流法的計(jì)算機(jī)處理程序,可以便捷地進(jìn)行編譜分析。(三)疲勞強(qiáng)度校核:設(shè)計(jì)中為保證不發(fā)生疲勞破壞,需D1,即 (14-29)由式(4-18)得 (14-30)(14-29)左邊分子與分母同乘以im并結(jié)合(14-30),可得安全強(qiáng)度條件故等效應(yīng)力d為 (14-31)安全系數(shù) (14-32)式中,N0S-N曲線的拐點(diǎn)對應(yīng)的循環(huán)數(shù);-1 材料疲勞極限;m式(14-8)中的指數(shù);i 第i級應(yīng)力水平的應(yīng)力幅;Ni 第i級應(yīng)力水平的循環(huán)應(yīng)力作用下,材料達(dá)到破壞時(shí)的應(yīng)力循環(huán)次數(shù);N 設(shè)計(jì)疲勞壽命即總應(yīng)力循環(huán)次數(shù);ni 在設(shè)計(jì)疲勞壽命下第
38、i級應(yīng)力水平的循環(huán)次數(shù);ni/N 第i級應(yīng)力的循環(huán)次數(shù)與總應(yīng)力循環(huán)次數(shù)之比,當(dāng)載荷譜已知時(shí)為一不變值;K-iD同前??梢婋S著設(shè)計(jì)壽命的增加,等效應(yīng)力增大而安全系數(shù)降低。(四)疲勞壽命估算:根據(jù)邁因納理論,達(dá)到疲勞破壞時(shí)有 (14-33)式中,NT為載荷譜下出現(xiàn)損傷的循環(huán)次數(shù)即所求的總壽命;ni為i級應(yīng)力水平i的循環(huán)次數(shù);i為i級應(yīng)力水平i的循環(huán)次數(shù)在總壽命中所占比例;Ni表示在應(yīng)力i作用下導(dǎo)致破壞的循環(huán)數(shù)。在應(yīng)力譜已知的情況下,Ni的估算是此項(xiàng)估算工作的關(guān)鍵。對于每級應(yīng)力水平下導(dǎo)致的破壞循環(huán)壽命的確定,可參照工程標(biāo)準(zhǔn),許多軟件安排了一些常用的準(zhǔn)則供用戶選用。這里僅以I-Deas為例,即:(1)
39、 應(yīng)力-壽命(Stress life)準(zhǔn)則(2) 應(yīng)變-壽命(Strain life)準(zhǔn)則(3) SWT準(zhǔn)則(Smith-WatsonTopper)(4) 美國機(jī)械工程學(xué)會(huì)(ASME)鍋爐和壓力容器規(guī)范(5) 英國焊接研究所(BWI)公式(Btitish Weld Institute formulation)另外,它還允許用戶自定義些特殊的應(yīng)力或應(yīng)變壽命準(zhǔn)則,程序?yàn)榇艘蚜粲邢鄳?yīng)的接口。以應(yīng)力-壽命(Stress life)準(zhǔn)則確定Ni,是依據(jù)材料的應(yīng)力壽命曲線或零件本身的應(yīng)力壽命曲線的斜線部分來確定。首先可用應(yīng)變片測定危險(xiǎn)點(diǎn)處的應(yīng)力或用材料力學(xué)或有限元等方法求出危險(xiǎn)點(diǎn)的應(yīng)力幅a,然后再根據(jù)斜線
40、部分求出對應(yīng)于應(yīng)力水平K-1Di時(shí)的斷裂壽命即為所求Ni。如果使用零件的S-N曲線進(jìn)行計(jì)算則可直接根據(jù)此曲線求得對應(yīng)于應(yīng)力幅a的Ni。也可先根據(jù)材料的S-N曲線等現(xiàn)有資料對材料的S-N曲線進(jìn)行修整從而得到畫出零件的S-N曲線,然后進(jìn)行與上相同的Ni的計(jì)算。在以上三種方法中,要根據(jù)所掌握資料的情況,優(yōu)先選擇最接近所設(shè)計(jì)對象的一種。三、復(fù)合應(yīng)力下的疲勞強(qiáng)度設(shè)計(jì)以上討論是單向應(yīng)力的情況,對于復(fù)合應(yīng)力的情況也也有類似的疲勞強(qiáng)度校核與疲勞壽命的估算方法,只是此時(shí)所用的應(yīng)力幅變成了對應(yīng)強(qiáng)度理論下的等效應(yīng)力幅,下面作一簡單討論。在構(gòu)件危險(xiǎn)點(diǎn)處的應(yīng)力分別為sx、sy、sz、txy、tyz、tzx時(shí),該處的第三
41、、第四強(qiáng)度理論的等效應(yīng)力分別為 (14-34) (14-35)用主應(yīng)力表示時(shí),分別有 (14-36) (14-37)這時(shí)的強(qiáng)度條件的一般表式為 (14-38)式中,KsD、s-1、sd為疲勞強(qiáng)度降低系數(shù)、材料的疲勞極限和對應(yīng)的等效應(yīng)力。試驗(yàn)表明,在平面彎扭組合疲勞應(yīng)力s、t的情況下,高當(dāng)材料達(dá)到疲勞破壞時(shí)滿足如下方程 (14-39)式中,s-1、t-1分別為材料的彎曲和扭轉(zhuǎn)的疲勞極限,此式由高夫首先提出。該式兩邊同乘以s-1并開方,有對于s-1、t-1,在第三、第四強(qiáng)度理論時(shí)分別有, (14-40)故上式又可變?yōu)?(14-41) (14-42)式(14-39)式(14-40)正好是式(14-3
42、2)和式(14-33)在平面彎扭組合情況下的結(jié)果。由零件的疲勞強(qiáng)度校核條件式(14-36)及式(14-38),有 (14-43)設(shè)ns=s-1/s,nt=t-1/s-1,分別為純彎和純扭轉(zhuǎn)時(shí)安全系數(shù),則上式為 (14-44)以上疲勞強(qiáng)度校核公式適用于鋼等延性材料,載荷為對稱循環(huán)。對于非對稱循環(huán)載荷,有類似公式 (14-45)式中,srd應(yīng)力比為r時(shí)的等效應(yīng)力 (14-46)式中,平均應(yīng)力折算系數(shù),見式(14-26)。第五節(jié) 如何用有限元法進(jìn)行疲勞分析一、有限元法疲勞分析的基本思路用有限元法進(jìn)行疲勞分析,其基本思路是:首先進(jìn)行靜或動(dòng)強(qiáng)度分析,然后進(jìn)入到后處理器取出相關(guān)的應(yīng)力應(yīng)變結(jié)果,在后處理器中
43、再定義載荷事件,循環(huán)材料特性,接著根據(jù)所需要的疲勞準(zhǔn)則對每一個(gè)載荷事件進(jìn)行壽命計(jì)算,最后根據(jù)累計(jì)損傷理論判斷是否開始破壞。由于結(jié)構(gòu)受力狀態(tài)往往是一復(fù)雜的應(yīng)力狀態(tài),而在實(shí)驗(yàn)中測得的結(jié)構(gòu)材料S-N曲線又常是在簡單應(yīng)力狀態(tài)下獲得的,因此常用最小能量屈服準(zhǔn)則或其它等效準(zhǔn)則,將所研究的疲勞點(diǎn)上的復(fù)雜應(yīng)力用一個(gè)等效應(yīng)力替代。對有限元法而言,這一過程很容易實(shí)現(xiàn)。等效替代以后,即可參照原始材料的S-N曲線進(jìn)行疲勞壽命評估。上述方法稱之為應(yīng)力-壽命法或S-N法,該方法不嚴(yán)格區(qū)分裂紋產(chǎn)生和裂紋擴(kuò)展,而是給出結(jié)構(gòu)發(fā)生突然失效前的全壽命估計(jì)。當(dāng)然,還可以采用更加現(xiàn)代化的局部應(yīng)變法或初始裂紋法。因篇幅所限,下面結(jié)合I-
44、Deas軟件,僅討論S-N法。二、I-DEAS 疲勞分析I-DEAS軟件可以進(jìn)行靜態(tài)疲勞分析(Static Durability Analysis)、瞬態(tài)疲勞分析(Transient Durability Analysis)。由于車輛結(jié)構(gòu)的零部件屬于低應(yīng)力、高循環(huán)疲勞,故常使用Stress life準(zhǔn)則,并使用修正Goodman圖,此時(shí),S-N曲線的經(jīng)驗(yàn)公式修正為: (14-47)計(jì)算中需要的材料參數(shù)包括:彈性模量、疲勞強(qiáng)度系數(shù)、疲勞強(qiáng)度指數(shù)、強(qiáng)度極限。 其具體的分析過程是:1 建立物理模型(Physical Model)對于疲勞分析來說,物理模型即包含結(jié)點(diǎn)、單元、物理特性和材料特性的有限元模
45、型。PhysicalModelMathematicalModelLoadingConditionsEventEvaluationPost Processing圖14-7 定義事件流程圖2 建立數(shù)學(xué)模型(Mathematical Model)數(shù)學(xué)模型也就是使用物理模型計(jì)算應(yīng)力或應(yīng)變。可通過 Model Solution或其它求解器來建立。求解后,可從后處理器中獲取相關(guān)的應(yīng)力或應(yīng)變。3 荷工況(Loading Conditions)對于靜態(tài)疲勞分析來說,可以用建立載荷函數(shù)的方式施加載荷。4 定義事件(Events)在進(jìn)行疲勞評估之前,必須先定義事件。它由物理模型、數(shù)學(xué)模型、載荷工況組成,如圖14-
46、7所示。5 評估(Evaluation)一般來說,我們可進(jìn)行下列估算:l 事件損傷(Event Damage)l 事件損傷方向(Event Damage Direction)l 損傷累積(Accumulated Damage)l 事件壽命估算(Event Life Estimate)6 后處理(Post Processing)疲勞分析的后處理與靜力學(xué)的后處理完全一致,此處不再重復(fù)。第六節(jié)實(shí)例分析一、搖枕的疲勞累積損傷分析及結(jié)果評價(jià)選擇一個(gè)轉(zhuǎn)向架搖枕進(jìn)行疲勞分析,并參照TB/T1959-91鐵道貨車鑄鋼搖枕試驗(yàn)評定方法進(jìn)行。圖 14-8 搖枕(俯視圖)圖 14-9 搖枕(仰視圖)(一)試驗(yàn)載荷B
47、1B2R2.3P0.32P1.0P其中:P一個(gè)轉(zhuǎn)向架承受的總載荷 P=(2x軸重-轉(zhuǎn)向架自重)·g(KN) P=444.4KNB1B2R1022.1KN142.21KN444.4KN搖枕側(cè)滾載、浮沉載荷曲線及加載位置如圖14-10,載荷R在旁承Z、Z點(diǎn)交替進(jìn)行加載,載荷B1、B2在心盤Q點(diǎn)進(jìn)行加載。(a)加載位置(b)側(cè)滾與浮沉載荷圖14-10 側(cè)滾與浮沉載荷加載位置側(cè)滾頻率為:1.25Hz浮沉頻率為:5.0Hz搖枕加載程序單元載 荷循環(huán)次數(shù)側(cè)滾載荷循環(huán)(Z-Z)25,000浮沉載荷循環(huán)(作用于心盤中心Q)75,000總 計(jì)100,000搖枕最低限度循環(huán)次數(shù)載 荷 型 式循環(huán)次數(shù)側(cè)滾
48、載荷循環(huán)(Z-Z)175,000浮沉載荷循環(huán)(作用于心盤中心Q)525,000總 計(jì)700,000(二)搖枕疲勞分析過程()對搖枕劃分有限元網(wǎng)格后,在Z、Z、Q點(diǎn)按照靜力學(xué)求解方式分別建立Load Set,并求解。()建立側(cè)滾載荷函數(shù)f_cycle_z、f_cycle_z1、和沉浮載荷函數(shù)f_cycle_q。()將f_cycle_z、f_cycle_z1分別施加于Z、Z,形成一個(gè)事件,設(shè)定循環(huán)次數(shù)為25000,計(jì)算其損傷。()進(jìn)入Post Process,檢查結(jié)果。若累積損傷<1,說明未損傷;若累積損傷1,則認(rèn)為結(jié)構(gòu)已經(jīng)破壞。()將f_cycle_q施加于Q,形成一個(gè)事件,設(shè)定循環(huán)次數(shù)為75000,計(jì)算其損傷及與上一事件的累積損傷。()進(jìn)入Post Process,檢查結(jié)果。若累積損傷<1,說明未損傷;若累積損傷1
溫馨提示
- 1. 本站所有資源如無特殊說明,都需要本地電腦安裝OFFICE2007和PDF閱讀器。圖紙軟件為CAD,CAXA,PROE,UG,SolidWorks等.壓縮文件請下載最新的WinRAR軟件解壓。
- 2. 本站的文檔不包含任何第三方提供的附件圖紙等,如果需要附件,請聯(lián)系上傳者。文件的所有權(quán)益歸上傳用戶所有。
- 3. 本站RAR壓縮包中若帶圖紙,網(wǎng)頁內(nèi)容里面會(huì)有圖紙預(yù)覽,若沒有圖紙預(yù)覽就沒有圖紙。
- 4. 未經(jīng)權(quán)益所有人同意不得將文件中的內(nèi)容挪作商業(yè)或盈利用途。
- 5. 人人文庫網(wǎng)僅提供信息存儲空間,僅對用戶上傳內(nèi)容的表現(xiàn)方式做保護(hù)處理,對用戶上傳分享的文檔內(nèi)容本身不做任何修改或編輯,并不能對任何下載內(nèi)容負(fù)責(zé)。
- 6. 下載文件中如有侵權(quán)或不適當(dāng)內(nèi)容,請與我們聯(lián)系,我們立即糾正。
- 7. 本站不保證下載資源的準(zhǔn)確性、安全性和完整性, 同時(shí)也不承擔(dān)用戶因使用這些下載資源對自己和他人造成任何形式的傷害或損失。
最新文檔
- 風(fēng)險(xiǎn)管理的制度與流程構(gòu)建試題及答案
- 網(wǎng)絡(luò)優(yōu)化測試的基本原則與方法試題及答案
- 2025屆上海外國語大附屬外國語學(xué)校數(shù)學(xué)八下期末達(dá)標(biāo)檢測試題含解析
- 盤點(diǎn)2025年VB考試回顧及試題及答案
- 電子文檔處理與管理技巧試題及答案
- 軟件設(shè)計(jì)師考試合作與協(xié)同工具試題及答案
- 有效利用閑置資源提升生產(chǎn)力計(jì)劃
- 未來市場競爭格局的戰(zhàn)略調(diào)整試題及答案
- 美術(shù)教育心理學(xué)培訓(xùn)活動(dòng)計(jì)劃
- 鄉(xiāng)鎮(zhèn)商圈保安工作總結(jié)與發(fā)展計(jì)劃
- 23G409先張法預(yù)應(yīng)力混凝土管樁
- MOOC 大學(xué)體育-華中科技大學(xué) 中國大學(xué)慕課答案
- [安徽]高速公路改擴(kuò)建工程交通組織方案(155頁)
- 父權(quán)制度下埃德娜的精神覺醒-精品文檔資料
- 張齊華:《平均數(shù)》課件
- 用藥情況記錄表正式版
- 《鐵路線路里程斷鏈設(shè)置和管理規(guī)定》
- 21世紀(jì)音樂教育發(fā)展趨勢——問題與對策2004年音樂教育國際學(xué)術(shù)會(huì)議在上海音樂學(xué)院召開
- 提高鋼管樁接頭焊接質(zhì)量圖文
- 中國字-中國人-歌詞
- 結(jié)構(gòu)工程師面試精彩試題及問題詳解
評論
0/150
提交評論